The 5S principles can greatly increase team and organizational efficiency. Using the 5S methodology, companies can create a safe, orderly work environment and workflow processes. Ultimately, this leads to continuous improvement of a team’s work. Originating from Japanese business culture, the 5S principles can be adapted to enhance team performance in contemporary work environments throughout the world.
In this article, we’ll discuss the 5S principles and how to employ them to strengthen your organizational processes. Learn how to employ the 5S methodology to benefit your team’s performance management while enhancing employee satisfaction and engagement.
Table of Contents
1. Understanding the 5S Principles
2. Benefits of 5S in Modern Workplaces
3. Applying 5S to Team Performance Management
4. Challenges and Considerations
Understanding the Japanese 5S Principles
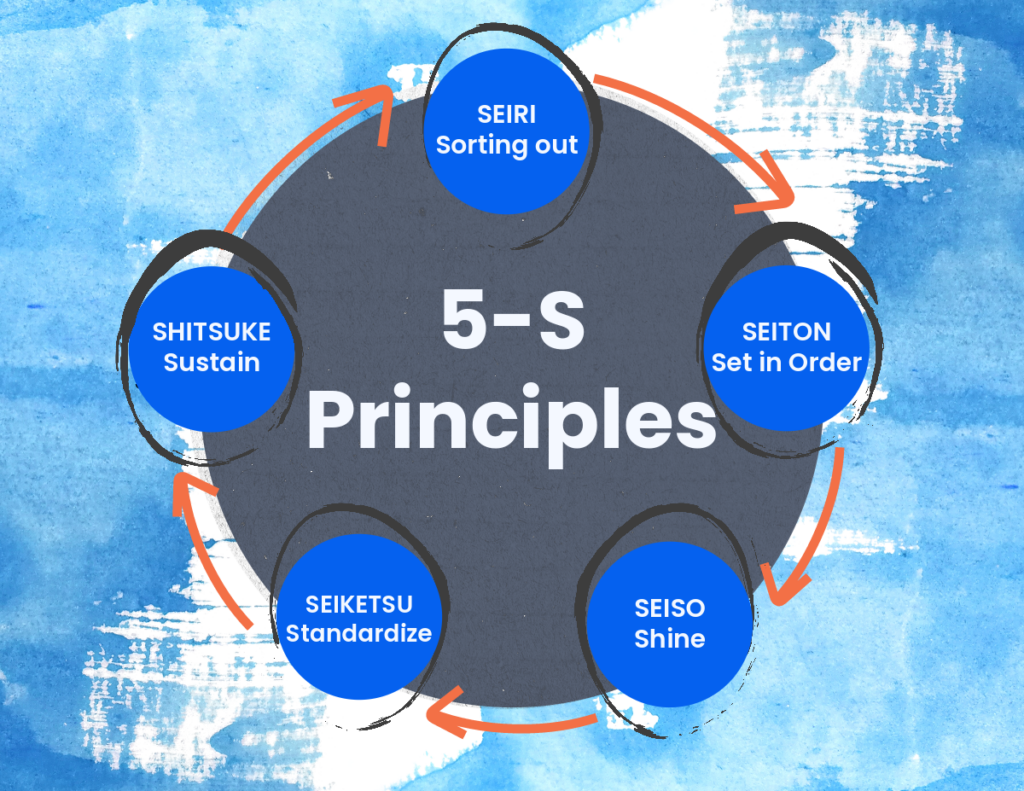
The 5S principles were initially developed to streamline Toyota’s vehicle production. “5S originated with Japanese inventor Sakichi Toyoda—the founder of Toyota, who is also known as the ‘father of the Japanese industrial revolution,’” reports Fast Company. Over the years, the 5S principles have been used not only in factories but across various industries, from software development to architecture.
What do the 5S principles entail? We’ll briefly walk through each of them here.
- 整理 Seiri (“sort”): Decluttering by eliminating unnecessary tools and materials. Essentially, this creates a user-friendly work environment, avoiding time spent searching for supplies. The same principle can be applied to team duties by carefully organizing tasks to eliminate redundant and unnecessary activities.
- 整頓 Seiton (“set in order”): Arranging the remaining resources and workflows in an orderly fashion to promote efficiency. This means assigning a proper place to all the necessary materials, keeping them in plain sight or easily accessible. In regard to job responsibilities, it means clarifying tasks and workflow.
- 清掃 Seiso (“shine”): Maintaining a neat and error-free work environment, both physically and digitally. This means cleaning and optimizing the space routinely.
- 清潔 Seiketsu (“standardize”): Implementing standard processes for conducting seiri, seiton, and seiso on a daily basis, which leads to consistency in performance.
- 躾 Shitsuke (“sustain”): Maintaining the established standards in a disciplined way, making them part of the daily routine so they’ll become habit.
These five principles will strengthen team performance when used consistently. Now, let’s explore the major benefits of using the 5S framework.
Benefits of 5S in Modern Workplaces
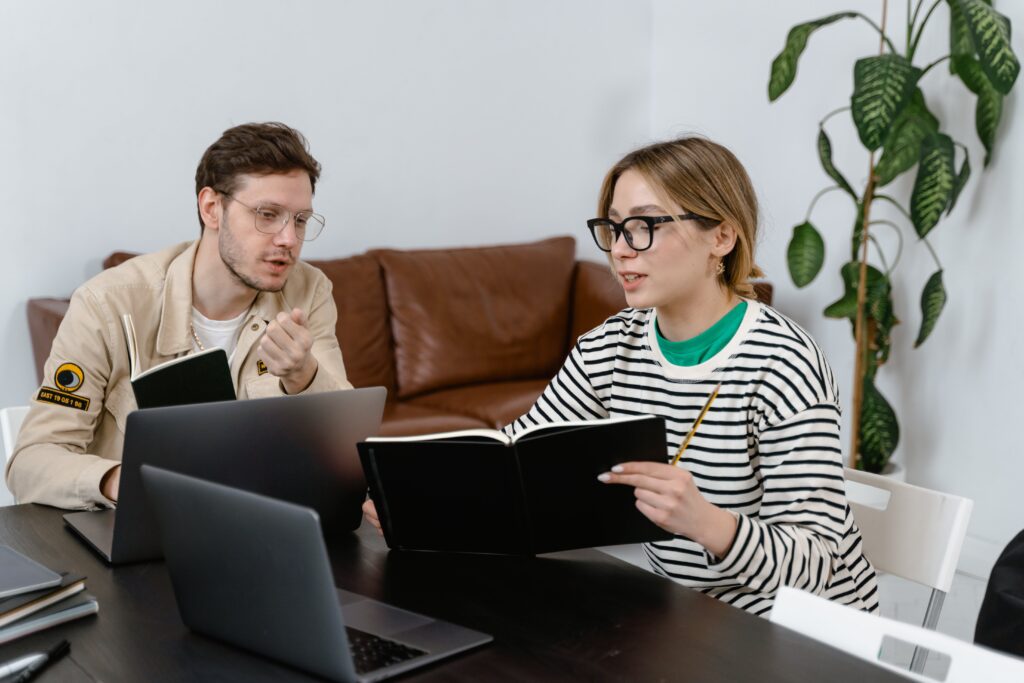
The 5S principles can aid in improving team efficiency, productivity, and overall performance. Ultimately, the consistency and team harmony they foster can contribute to a positive work culture and employee satisfaction. Let’s discuss some specific ways in which they further these objectives.
Enhancing Quality
The 5S principles can help organizations achieve consistent high quality in products and services. Ultimately, this promotes continuous improvement and increases organizational success.
Reducing Waste
The 5S principles tend to appeal to those who embrace lean methodologies, as they help reduce wasted time, effort, and resources. By prioritizing thoughtful organization and standardized systems, they help teams avoid redundant work. Through waste reduction, the 5S principles can also improve the sustainability of business operations.
Improving Safety
A tidy workplace and clear, streamlined processes reduce safety hazards—one of the key reasons why Toyota implemented the system in the first place. Many manufacturing companies utilize the 5S principles for this reason.
Strengthening the Employee Experience
When teams employ the 5S principles, employees have greater clarity about their tasks and role. In turn, they’ll reach their goals more effectively. They’ll take more pride and satisfaction from their work as a result.
The 5S methodology can help your team make great strides in all of these areas. Ultimately, these benefits can even increase retention and long-term organizational success.
Applying 5S to Team Performance Management
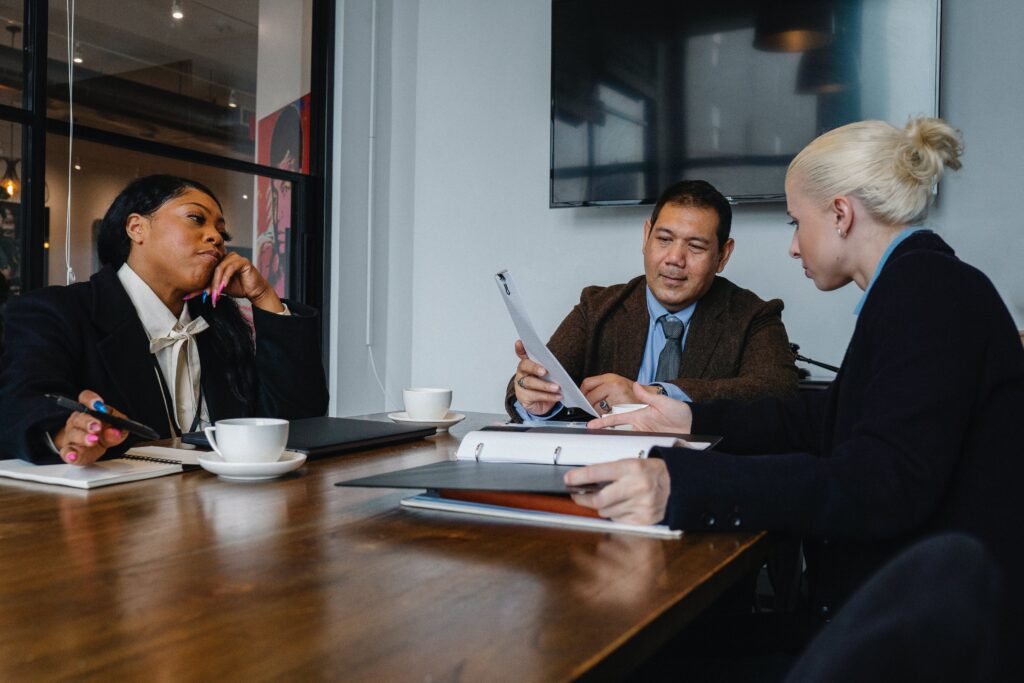
As an HR or company leader, you can translate 5S principles into team management practices. In particular, Low Sui‐Pheng and Sarah Danielle Khoo outline 7 key steps for implementing the 5S principles in their research published in Team Performance Management:
- Get buy-in from top management
- Become informed about the 5S principles
- Train the trainers (your HR staff, leaders, and managers)
- Conduct a promotional campaign to build investment and education
- Launch the 5S campaign, providing ongoing training
- Monitor and evaluate your success
- Maintain the system, adapting as needed
As you plan and implement your 5S campaign, centre these five priority areas in your efforts. They’ll help you thoroughly understand, document, and enact the changes you need to make, while building investment at all levels.
Audit Your Processes (and Environment)
To implement the 5S principles, audit the tasks and responsibilities of the team to pinpoint areas where energy or resources are wasted. Which processes, documents, or environments are overly complicated or messy? Involve all team members in this process, asking for their perspectives. Then work to eliminate any redundant or unnecessary steps, tasks, or elements. Make sure each person understands the tasks on their plate, too, which will also help work flow more efficiently.
Foster Continuous Improvement
Creating a standardized and long-lasting system requires full employee participation, Sui‐Pheng and Khoo note. “For self-sustaining progress, all employees should be encouraged to identify their own problems and formulate their own solutions for continuous improvement,” they assert. Train all employees in how to use the 5S principles so they can seek out ways to streamline tasks and processes.
Standardize Best Practices
During step 4—seiketsu, or “standardize”—draw up best practices for the first three steps, says Adobe. Create quick-reference checklists for teams to use as well. “During the Standardize step, make it a point to gather feedback from your team members,” they add. “Sharing what one team learns with other teams will help you refine and spread your best practices across the entire organization.”
Make It Sustainable
According to the EPA, the shitsuke (“sustain”) step is usually the hardest of the 5S principles. To make these principles a habit, use signs, posters, quick-reference manuals, and newsletter updates to reinforce key messages. Integrate them into team check-ins and manager one-on-ones, as well as performance reviews, they add. By using different formats to emphasize your message, you’ll help your team build new ways of working.
Use Supportive Tools
Use HR tools to support your 5S launch by enhancing efficiency and minimizing wasted effort. For example, goal-tracking software can help employees focus on the right priorities. Performance evaluation tools can simplify and standardize the appraisal process while cutting down significantly on the time required from managers. And good analytics tools will help you easily monitor progress and make sense of your data.
Challenges and Considerations
Implementing 5S principles in diverse and dynamic modern work environments can sometimes bring challenges. Let’s explore how to overcome several key ones.
Resistance to Change
People may feel they already have a good working method and be reluctant to change. If a new leader is proposing the changes, they may even be resentful of the idea. Some may feel the leader believes they aren’t being conscientious enough.
Approach the topic by emphasizing that the 5S methodology can help even the most conscientious people become even better. Emphasize the need to standardize these best practices. A leader could spend time talking with employees about avenues for process improvement before launching the system to build investment, too.
Cultural Differences
Employees and managers could perceive the 5S principles as clashing with their existing culture. While the 5S methodology aligns well with Japanese business culture, it could clash with workplace norms in some companies. Emphasize that these principles can help you make positive cultural adjustments while maintaining the core components of your culture that make you unique.
Review the core values of your company. Then find the ways in which they connect to the 5S principles. If you have a culture that embraces messiness, for example, perhaps you truly value creativity. Emphasize how a tidier workspace can promote the realization of that value.
Lack of Investment
In other cases, people may not perceive the full value of the 5S methodology. Educating them on the benefits and training them to apply the 5S principles effectively will boost engagement. Leaders should emphasize how the 5S methodology will strengthen the business as a whole.
With determination, strong communication, and clear training, you can overcome any of these hurdles and successfully leverage the 5S principles. Let’s explore some examples of companies that have done so.
Real-World Examples
Countless organizations have successfully integrated 5S into their team performance management. For example, Kaiser Permanente Colorado used 5S principles to improve their Medicaid enrollment template and process, says the American Society for Quality (ASQ). They weeded out unnecessary fields from their template, reorganized them with input from stakeholders, and developed a Microsoft Access database that prevented duplicate entries. Then, they standardized this spreadsheet for future use and designed a clear system for using Access and Excel templates.
“The three-month project resulted in a 45 percent gain in Medicaid membership while increasing Medicaid revenue by more than $1 million annually and decreasing cycle time for member enrollment from 62 days to 11 days,” writes ASQ.
Harley Davidson famously used the 5S principles to escape near-bankruptcy and make an incredible rebound in 1985. In fact, they increased productivity by 50% and reduced space requirements by 25%, says Dantar P. Oosterwal in The Lean Machine. Like Toyota, they prioritize just-in-time production to avoid creating wasted inventory, as well as insight from team members on how to continuously improve operations.
Some medical facilities follow the 5S principles as well. By improving efficiency and orderliness, they promote patient safety.
Consider how you can start applying the 5S methodology to enhance your own organization’s performance. Leveraging these principles from Japanese business culture can help your organization achieve continuous improvement. Employee satisfaction will increase as you streamline workflow processes and enhance team performance, too.
Learn how software can enhance team performance management—demo our product.